These days, almost everything we buy is produced in factories, the very backbone of the global economy and our modern way of life. Yet most ordinary consumers never set foot inside these marvels of 21st-century engineering, robotics, and computer automation. Technology has significantly reduced the need for human input in day-to-day operations. But a lot of time, money and effort is still required to keep them running smoothly, safely, and efficiently. This is especially true of food production plants, which must comply with strict hygiene standards.
In Japan, factories are today facing a shortage of skilled maintenance technicians. This is an area where physical, on-site inspections are still the norm. Moreover, technicians often have to travel long distances to visit sites, and service records may be distributed across multiple locations. To Ajinomoto Engineering Co. (AJEC), which has a proven track record in designing, building, operating, and maintaining production facilities for the food industry, these challenges represented a golden opportunity.
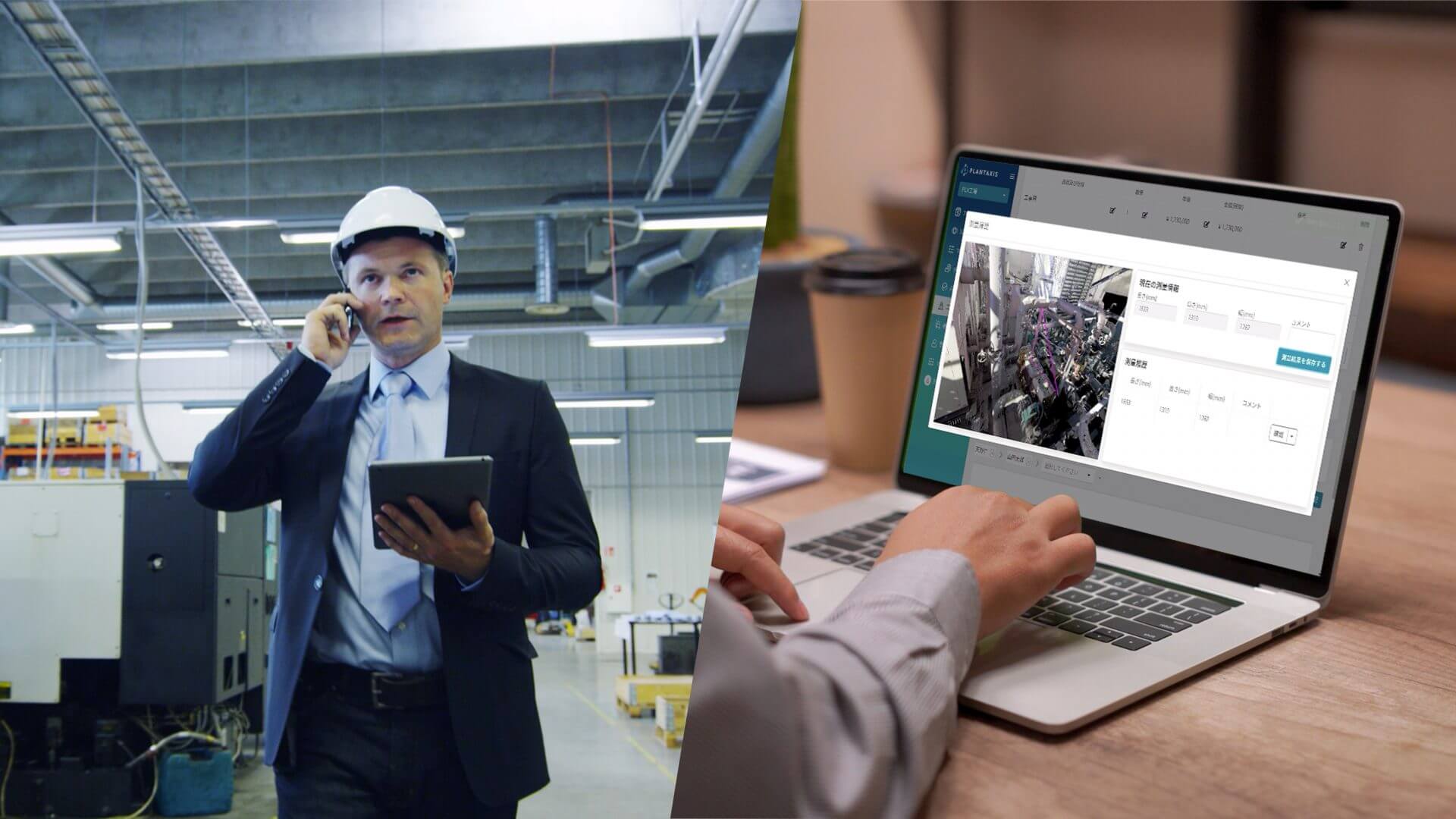
AJEC teamed up with cutting-edge software company Elysium to apply 3D scanning and point cloud technology to develop a new digital platform called PLANTAXIS® that acts as a hub, or “axis,” for plant management, featuring an intuitively designed and highly detailed 3D interface for PCs and tablets. Clients can easily create and execute maintenance plans and take measurements or order parts remotely. They’re also supported with data entry and periodic analysis services performed by qualified maintenance engineers. Since PLANTAXIS® enables remote access and sharing of data, it not only improves the efficiency of operations, it also saves labor and could help extend the life of the plant.
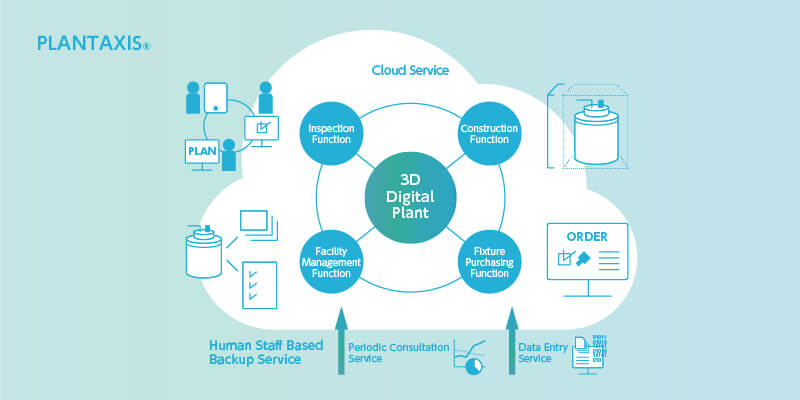
AJEC Director and Managing Executive Officer Fumihiro Kobayashi and his colleague Takayuki Kobayashi (no relation) came up with the business model—but they didn’t do it all on their own. They started with just an idea and a lot of enthusiasm. Having quickly recognized the huge potential of 3D scanning technology for their industry, they began investigating the right way to commercialize it. They realized that to be competitive, they needed to focus on AJEC’s core competency while offering a product and service that others in their industry couldn’t easily imitate—and quickly.
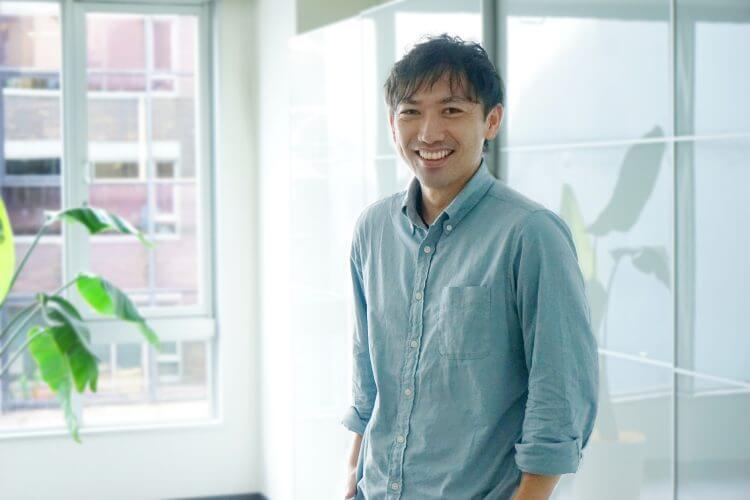
Takayuki Kobayashi implemented Agile project management to keep things moving fast and reacting to the real needs of users.
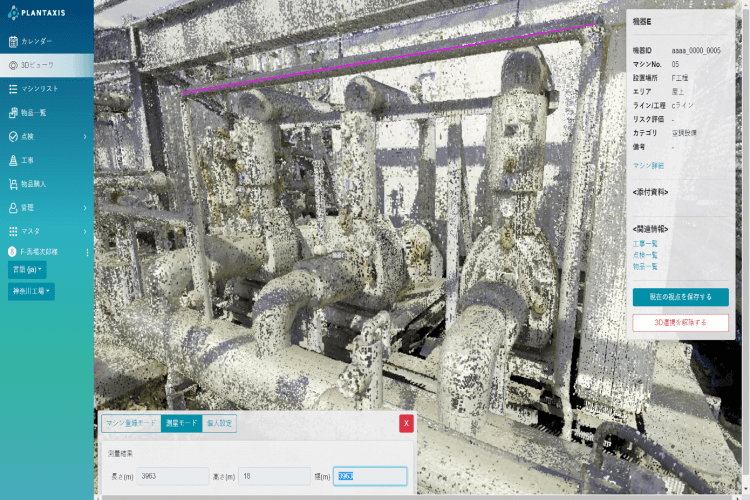
The captured image data from the facility is directly registered within the system as 3D data.
Their agile approach incorporated input from stakeholders, including Elysium, web designers, cloud service providers, and plant operators. “It was a bit like a role-playing game,” says Fumihiro Kobayashi. “At every stage we met new people who helped us move forward, and we ended up a long way from where we started.” Ultimately, they were able to deliver a finished product in just eight months from kickoff to launch. Takayuki Kobayashi credits their rapid success to the team’s small size, which streamlined decision making, and the Ajinomoto Group’s pioneering spirit, which gave them the confidence to pursue their quest despite the unfamiliarity of the terrain. The launch of PLANTAXIS®, which happened just as the COVID-19 pandemic was beginning to restrict people’s movements, has proven timely.
Several members of the Ajinomoto Group are now planning to implement PLANTAXIS® in their facilities. With its potential to enable factories to run more efficiently and to support the food supply and human health, the service is generating a high level of interest within the food industry and beyond.